Review What involves sensing conditions and predicting what conditions will require actions?
Mẹo về What involves sensing conditions and predicting what conditions will require actions? 2022
Bùi Văn Quân đang tìm kiếm từ khóa What involves sensing conditions and predicting what conditions will require actions? được Cập Nhật vào lúc : 2022-11-13 04:34:03 . Với phương châm chia sẻ Bí quyết về trong nội dung bài viết một cách Chi Tiết Mới Nhất. Nếu sau khi đọc Post vẫn ko hiểu thì hoàn toàn có thể lại Comment ở cuối bài để Tác giả lý giải và hướng dẫn lại nha.Condition monitoring
Nội dung chính Show- Condition monitoringCondition monitoringIntroducing condition monitoringSensor Materials, Technologies and ApplicationsFormation of Digital Mine Using the Internet of Things6.9 Condition Monitoring of Mine MachineryMaintenance
Management5.5.5.4 Condition Monitoring Surveillance RoundInnovative smart scheduling and predictive maintenance techniquesCondition monitoringCompressorsCondition MonitoringCondition monitoring of rotating machines using on-shaft vibration measurementAdvances in Machine Learning and Data Analytics1.4 Brief information of intelligent data analytics for condition monitoringMaintenance information systems8.3.13 Condition monitoringWhat do you call conditions that an acceptable solution must provide?What type of control makes sure that the tasks of the organization are being conducted efficiently and effectively?What is the most critical phase in the decision making process?What type of decisions are novel?
Juan Carlos A. Jauregui Correa, Alejandro A. Lozano Guzman, in Mechanical Vibrations and Condition Monitoring, 2022
Abstract
Condition monitoring is an evolution of predictive maintenance or proactive maintenance. The origin is difficult to define, but predictive maintenance has made enormous progress over the last few decades. Nowadays, it has been addressed as one of the most innovative solutions for anticipating failures in machinery and is being used by a wide variety of industrial sectors. Prediction maintenance could be applied to a large industrial sector when the cost of vibration sensors is competitive. This advantage reduced the cost of failures in comparison with the investment in the measurement equipment and analysis system. In the beginning, the systems were rudimentary and required specialized personnel to collect data and make the analysis. The convergence of high-precision accelerometers and the ability to process the Fourier transform with the FFT algorithm allowed the development of rapid tools that can make a diagnosis on the actual condition of machines. Previously, vibration sensors were applied in a few types of equipment due to their cost and the need for specialized personnel. These first concepts were complemented with other emerging technologies such as ultrasonic, thermography, acoustic sensors, and directional microphones.
Read full chapter
URL: https://www.sciencedirect.com/science/article/pii/B9780128197967000081
Condition monitoring
In Tribology Handbook (Second Edition), 1995
Introducing condition monitoring
If an organisation has been operating with breakdown maintenance or regular planned maintenance, a change over to condition-based maintenance can result in major improvements in plant availability and in reduced costs. There are, however, up front costs for organisation and training and for the purchase of appropriate instrumentation. There are operational circumstances which can favour or retard the potential for the introduction of condition-based maintenance.
Table 11.2. Factors which can assist the introduction of condition-based maintenance
FactorMechanism of actionWhere a safety risk is particularly likely to arise from the breakdown of machinery Typical examples are plant handling dangerous materials, and machines for the transport of people. Where accurate advanced planning of maintenance is essential Typical examples are equipment situated in a remote place which is visited only occasionally for maintenance, and mobile equipment which makes only occasional visits to its base. Where plant or equipment is of recent design, and may have some residual development problems Condition monitoring enables faults to be detected early while damage is still slight, thus providing useful evidence to guide design improvements. It also improves the negotiating position with the plant manufacturer. Where relatively insensitive operators use expensive equipment whose breakdown may result in serious damage Condition monitoring enables a fault to be detected in sufficient time for an instruction to be issued for the withdrawal of the equipment before expensive damage is done. Where the manufacturer can offer a condition monitoring service to several users of his equipment The cost to each user can be reduced in this way, and the manufacturer gets a useful feed-back to guide his product design and development. Where instruments or other equipment required for condition monitoring can be used, or is already being used, for another purpose Other applications of the instruments or equipment may be process control or some servicing activity such as rotor balancing.
Table 11.3. Factors which can retard the introduction of condition-based maintenance
FactorMechanism of actionWhere an industry is operating a low level of activity, or operates seasonally, so that plant and machinery is often idle If the plant is only operating part of the time, there is generally plenty of opportunity for inspection and maintenance during idle periods. Where there is too small a number of similar machines or components being monitored by one engineer or group of engineers to enable sufficient experience to be built up for the effective interpretation of readings and for correct decisions on their significance To gain experience in a reasonable time, the minimum number of machines tends to vary between 4 and 10 depending on the type of machine or component. The problem may be overcome by pooling monitoring services with other companies, or by involving machine manufacturers or external monitoring services. Where skilled operators have close physical contact with their machines, and can use their own senses for subjective monitoring Machine tools and ships can be examples of this situation, but any trends towards the use of less skilled operators or supervisory engineers, favours the application of condition monitoring.
Table 11.4. A procedure for setting up a plant condition monitoring activity
ActivityRemarks1. Check that the plant is large enough to justify having its own internal system. If the total plant value is less than £2M it may be worth sub-contracting the activity. 2. Consider the cost of setting up. For most plant, a setting up cost of l% of the plant value can be justified. If there is a major safety risk, up to 5% of the plant value may be appropriate. 3. Select the machines in the plant that should be monitored. The important machines for monitoring will tend to be those which:(a)
Are in continuous operation.
(b)Are involved in single stream processes.
(c)Have minimum parallel or stand-by capacity.
(d)Have the minimum product storage capacity on either side of them.
(e)Handle dangerous or toxic materials.
(f)Operate to particularly high pressures or speeds.
4. Select the components of the critical machines on which the monitoring needs to be focussed. The important components will be those where:(a)A failure is possible.
(b)The consequences of the failure are serious in terms of safety or machine operation.
(c)If a failure is allowed to occur the time required for a repair is likely to be long.
5. Choose the monitoring method or methods to be used. List the possible techniques for each critical component and try to settle for two or the most three techniques for use on the plant.Table 11.5. Problems which can arise
ProblemSolutionRegular measurements need to be taken, often for months or years before a critical situation arises. The operators can therefore get bored. The management need to keep the staff motivated by stressing the importance of their work. The use of portable electronic data collectors partially automates the collection process, provides a convenient interlace with a computer for data analysis, and can also monitor the tour of duty of the operators. One of the measurements indicates that an alert situation has arisen and a decision has to be made on whether to shut down the plant and incur high costs from loss of use, or whether it is a false alarm. To avoid this situation install least two physically different systems for monitoring really critical components, e.g. measure bearing temperature and vibration. In any sự kiện always recheck deviant readings and re-examine past trends. The operators take a long time to acquire the necessary experience in detection and diagnosis, and can create false alarms. Start taking the measurements while still operating a planned regular maintenance procedure. Take many measurements just prior to shut down and then check the components to see whether the diagnosis was correct.
Table 11.6. The benefits that can arise from the use of condition monitoring
BenefitMechanism1.
Increased plant availability resulting in greater output from the capital invested.
2.Reduced maintenance costs.
Machine running time can be increased by maximising the time between overhauls. Overhaul time can be reduced because the nature of the problem is known, and the spares and men can be ready. Consequential damage can be reduced or eliminated. 3.Improved operator and passenger safety.
The lead time given by condition monitoring enables machines to be stopped before they reach a critical condition, especially if instant shutdown is not permitted. 4.More efficient plant operation, and more consistent quality, obtained by matching the rate of output to the plant condition.
The operating load and speed on some machines can be varied to obtain a better compromise between output, and operating life to the next overhaul. 5.More effective negotiations with plant manufacturers or repairers, backed up by systematic measurements of plant condition.
Measurements of plant when new, the end of the guarantee period, and after overhaul, give useful comparative values. 6.Better customer relations following from the avoidance of inconvenient breakdowns which would otherwise have occurred.
The lead time given by condition monitoring enables such breakdowns to be avoided. 7.The opportunity to specify and design better plant in the future.
The recorded experience of the operation of the present machinery is used for this purpose.Read full chapter
URL: https://www.sciencedirect.com/science/article/pii/B9780750611985501028
Sensor Materials, Technologies and Applications
M.S.H. Bhuiyan, I.A. Choudhury, in Comprehensive Materials Processing, 2014
Abstract
Tool condition monitoring (TCM) has become indispensable to meet the increasing demand of unmanned machining for the modern automatic manufacturing. Sensor-based TCM is the latest addition to the TCM techniques. This chapter presents a review of some widely used TCM techniques based on some evaluation parameters like sensor type, data processing method, application, effectiveness, limitation, and setback. This review shows that different sensing techniques with pertinent data analyzing methods are more significant for any particular type of application. Recommendations are also made based on the articles reviewed as a direction for future research in TCM.
Read full chapter
URL: https://www.sciencedirect.com/science/article/pii/B9780080965321013303
Formation of Digital Mine Using the Internet of Things
S.K. Chaulya, G.M. Prasad, in Sensing and Monitoring Technologies for Mines and Hazardous Areas, 2022
6.9 Condition Monitoring of Mine Machinery
Mining machinery often work under nonstationary and time-varying load conditions. The concept of condition monitoring (CM) is an evolution of diagnostic and prognostic systems. The goal of CM of mining machinery is to examine its functional health. Real-time assessment of its functional health is useful for predicting fault in components/operation and thereby improving performance of equipment. For CM of mine machinery variety of transducers such as accelerometers, acoustic emission sensors, tachometers, thermocouples, etc., are subsequently segmented into discrete and coherent analysis intervals to extract feature vectors that are fed into pattern-recognition algorithms and post processing including diagnosis, prognosis, sensor-failure detection, and reporting (Figs. 6.20 and 6.21).
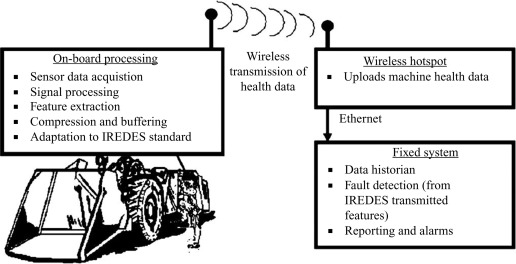
Fig. 6.20. Schematic of mine machinery monitoring system.

Fig. 6.21. Data flow diagram for data acquisition from mine machinery (Benedettini et al., 2009).
Monitoring and tracking of mining machinery using IoT provides a more convenient and secure management platform. IoT focuses on real-time monitoring of all measuring points of mechanical and electrical machinery. Each machine or equipment is equipped with sensors, RFID, controller, etc. Various information can be collected, stored, and processed. In addition, graphics and real-time data can be displayed. This work status of various types of underground mine equipment can be sent to the monitoring center on the ground in order to better control of equipment’s operation remotely for tracking, maintenance, troubleshooting, etc.
CM is a process of monitoring different parameters of condition in machinery (vibration, temperature, oil pressure, etc.) in order to identify any significant change, which is indicative of a developing fault. CM allows maintenance to be scheduled, as well as actions to be taken to prevent failure and avoid its consequences. CM techniques are normally used on rotating equipment and other machinery (pumps, electric motors, internal combustion engines, etc.), while periodic inspection using nondestructive testing techniques and fit-for-service evaluation are used for stationary equipment. The following list includes main CM techniques applied for mining equipment:
•vibration analysis and diagnosis of faults
•lubricant analysis
•scoustic emission (airborne ultrasound) study
•IR thermography
•ultrasound testing (material thickness/flaw testing)
•motor CM and motor current signature analysis
Vibration analysis is the most commonly used method for CM of rotating machines. Measurements are taken on machine-bearing casings with accelerometers (seismic or piezo-electric transducers) to measure casing vibrations, and are on the vast majority of critical machines, with eddy-current transducers that directly observe rotating shafts to measure radial and axial displacement of shaft. The level of vibration is compared with historical baseline values such as former startups and shutdowns, and in some cases, established standards such as load changes to assess the severity.
Most of the vibration analysis instruments today utilize a fast Fourier transform which is a special case of the generalized discrete Fourier transform and converts the vibration signal from its time domain representation to its equivalent frequency domain representation.
Heat is indicative of failing components, especially degrading electrical contacts and terminations. Thermography can also be successfully applied to high-speed bearings, fluid couplings, conveyor rollers, and storage tank internal build-up.
A carefully taken sample of debris is suspended in lubricating oil (taken from filters or magnetic chip detectors). When it is studied using a scanning electron microscope, it reveals the elements contained and their proportions, size, and structures. Using this method, the mechanical failure mechanism and time to eventual failure of machinery may be determined. Spectrographic oil analysis that shows chemical composition of oil, can be used to predict failure modes.
Ultrasound technique can be used in case of high- and slow-speed mechanical applications and high-pressure fluid situations. Digital ultrasonic meters measure high frequency signals from bearings and display result as a decibels per microvolt (dBuV) value. This value is used to predict increases in friction, rubbing and impacts, and know other bearing defects. It also helps to decide about proper intervals for re-lubrication.
Wear debris detection sensors are capable of detecting ferrous and nonferrous wear particles in lubrication oil giving considerable information about condition of the machinery. By monitoring a trend of what debris is being generated, it is possible to detect faults prior to catastrophic failure of rotating equipment.
Read full chapter
URL: https://www.sciencedirect.com/science/article/pii/B9780128031940000064
Maintenance Management
Michael Guy Deighton, in Facility Integrity Management, 2022
5.5.5.4 Condition Monitoring Surveillance Round
Condition monitoring surveillance rounds may be conducted by the FI&R group and are particularly focused on critical equipment. Usually these rounds are very detailed and could take up to a day for each round to be completed, depending on the amount of critical equipment and detail of each facility area. Typically, condition monitoring surveillance rounds are conducted on a monthly basis.
More often than not, the information is recorded directly onto a handheld device because of the volume of data that is collected and uploaded to a computer once the round is complete. The data is then analyzed and a report issued as necessary once the condition monitoring technician completes the round.
Read full chapter
URL: https://www.sciencedirect.com/science/article/pii/B978012801764700005X
Innovative smart scheduling and predictive maintenance techniques
Jinjiang Wang, Robert X. Gao, in Design and Operation of Production Networks for Mass Personalization in the Era of Cloud Technology, 2022
Condition monitoring
CM is mainly for real-time monitoring of equipment status (Hameed et al., 2009). Generally, the CM process includes two aspects: collecting equipment status information and understanding the causes and consequences of equipment failures and equipment degradation trends. The CM process can be performed when the equipment is running (online) or not (off-line) regular time intervals (periodically) or continuously. Periodic monitoring uses portable indicators, including hand-held meters, acoustic emission units, and vibration pens, etc., and even human senses, such as degree of dirtiness and abnormal colors while continuous monitoring mainly uses special measuring instruments (e.g., various sensors). Two main factors affecting continuous monitoring are cost and noise (Jardine et al., 2006). Because this type of monitoring requires a lot of special devices, and the continuous data stream will be doped with noise, which affects the quality of the signal. Similarly, there are also influencing factors for periodic monitoring, because there may be important information about equipment failures in the unmonitored time period.
There are many CM technologies in the literature and several of them are discussed below (Ahmad & Kamaruddin, 2012).
Read full chapter
URL: https://www.sciencedirect.com/science/article/pii/B9780128236574000075
Compressors
Michael S. Forsthoffer, in Forsthoffer's More Best Practices for Rotating Equipment, 2022
Condition Monitoring
Condition monitoring requirements for screw compressors should follow the principle of component condition monitoring. The following major components should be monitored:
■Rotor
■Journal bearing
■Thrust bearing
■Seals
The suggested minimal condition monitoring requirements are presented in Table 3.1.11.
Table 3.1.11. Minimum Condition Monitoring Required
■
Performance (rotor)
■Flow trend
■Efficiency check
■Manual vibration readings (accelerometers/velocity)
■Thrust bearing temperature measurement (rtd’s)
B.P. 3.2:When to use medium and high speed (>400 RPM) reciprocating compressors
Although it is generally recommended against using these types of Reciprocating Compressors in process units due to low inherent reliability and high maintenance costs, there is a very valuable application in which they are recommended.
That would be in upstream services in the gas exploration fields where the locations are remote with limited if any electricity available for a motor and wells are constantly changing. These compressors are typically used in the field as a package with a reciprocating gas engine, using the gas from the wells to drive it.
A huge advantage in this service would be the smaller footprint of this machine allowing it to be portable and moveable from one location to another in the gas fields. Most Users have least one spare ready to go in case one of their compressor packages has a failure one of the wells.
L.L. 3.2:Use of a medium or high speed reciprocating compressor in critical process units have resulted in very poor reliability
Due to the high speed, the packing, piston rings, bearings, and especially the valves will wear higher rates and the maintenance schedule increased. In a petrochemical plant or refinery where a critical compressor being shutdown equates to immediate loss of production, the larger frame/higher capital cost of a low speed compressor will pay itself off in the first year of operation.
Read full chapter
URL: https://www.sciencedirect.com/science/article/pii/B9780128092774000036
Condition monitoring of rotating machines using on-shaft vibration measurement
M.E. Elnady, ... S.O. Oyadiji, in 10th International Conference on Vibrations in Rotating Machinery, 2012
ABSTRACT
Condition monitoring of rotating machines enables early detection of faults and avoidance of unexpected machinery breakdowns. Vibration-based condition monitoring (VCM) is a well-known and well-accepted method for the health monitoring of rotating machines in industries. However the conventional VCM possesses some limitations in terms of using a number of vibration sensors each bearing pedestal and sufficient experience to interpret the measured vibration data to identify fault(s), if any, present in the machine. Hence the on-shaft vibration (OSV) measurement has been proposed in this study using a tiny Micro Electro Mechanical Systems (MEMS) accelerometer with a wireless node for the data transmission to the computer. This approach is expected to reduce the number of sensors used currently and may also contain enriched vibration information about the shaft which may ease the fault diagnosis process. The proposed OSV measurement approach is applied to a small experimental rig and then experiments were conducted with a few simulated faults in the rig. Initial observations indicate that the OSV measurement gives better classification of different machine states compared to the on-bearing one. The experimental results are discussed in the paper.
Read full chapter
URL: https://www.sciencedirect.com/science/article/pii/B978085709452050058X
Advances in Machine Learning and Data Analytics
Hasmat Malik, ... Atif Iqbal, in Intelligent Data-Analytics for Condition Monitoring, 2022
1.4 Brief information of intelligent data analytics for condition monitoring
The condition monitoring (CM) is a way or method of monitoring the health of the system, sub-system, and/or its associated equipments. CM can be performed by using any type of methods such as physics-based method, model-based method, and data-driven methods. The physics-based and model-based methods required system information, while data-driven method works on historical data captured with respect to the time varying interval. Generally, mechanical and/or electrical data generated with the help of sensor are used for CM of the machinery. There are some basic steps to perform the CM of a system/sub-system/its associated equipments, these are: (1) identify the critical assets with the system; (2) identify the parameters to be monitored and its sampling frequency rate; (3) identify the suitable CM solution/method; (4) demonstration/installation of the CM solution on site; and (5) integration of the CM system with the available maintenance solution in the system. There are some basic significant indications of the failure condition in the system/machinery. These indications are the vibration, noise, heat, smell, smoke, and finally breakdown condition. So, to prevent the system, doing CM in advanced level is not an easy task for the maintenance engineers. Generally, three types of maintenance scenarios (PdM: predictive maintenance, TBM: time based maintenance/planned maintenance, and RM: reactive maintenance) are performed for doing CM. Normally, the indication of failures (i.e., vibration, noise, heat, smell, smoke, and finally breakdown condition) come under RM, which is fixed after the system breaks. But system owner wants to fix failure condition before breaks. Under this situation, PdM and TBM play an important role so that cost of repair may reduce with respect to enhance the system performance.
Several types of CM techniques are utilized by the industry such as: (1) vibration based CM; (2) lubricating oil analysis based CM; (3) thermographic based CM; and (4) other methods (MCSA: motor current signature analysis). According to the market survey, the key contributions of these methods of CM are as per their ranked values: vibration CM, lubricating oil analysis, thermography, MCSA. While vibration based CM covers the market share more than 65% but the cost of analysis is higher than MCSA. The service market of CM is very good since 2022 to till now with higher growth rate of CAGR (compound annual growth rate). According to the market revenue of Europe region, Germany is the top followed by the United Kingdom, Italy, and France. In the Asia-Pacific region, China is the top followed by the Nhật bản and India. According to the current statistics, top service providers are GE Measurement & Control followed by SKF, Emerson, and Rockwell Automation.
The initiation of IDA/IBDA in the area of CM carries big market revenue of the business part. Since starting in 2000 and till date, IDA/IBDA is categorized into four phases. Phase-1 is in between 2000 and 2005, which is related to the asset management. Phase-2 belongs to the asset management & data reporting from 2005 to 2010. IDA/IBDA, and evaluation comes in phase-3 from 2010 to 2015 and finally phase-4 belongs to PdM or predictive analysis, which started in 2015 to till date. Moreover, in the future, prescriptive analytics may come in picture which would lead through digital twin technology. The prescriptive analysis mainly focuses on the future prediction of the equipment condition.
In the CM area following broad research area will come as energy monitoring, smart building monitoring, production/process monitoring, and environmental monitoring. In the energy monitoring, data coming from smart meters will be used for IDA/IBDA. In the area of smart building monitoring, data coming from air-conditioning system, boiler, sensors, etc., are used. The soil, water, air, and emission data monitoring comes under the environmental monitoring. Therefore, there are some key players which hold the key position in the market as per the method of CM. For example, in the area of MCSA, the key contributors are: Siemen AG ( top), ABB, Tập đoàn Mitsubishi, and Bosch Rexroth. In the area of thermography-based CM, the key contributors are: FLIR systems Inc ( top), Fluke corporation, and Nippon Avionics Co. In the area of lubrication oil based CM, the key contributors are: Bureau Veritas, Intertek Group, SGS, ALS Global, Spectro Scientific, TestOil, Parker Hannifin, GE, GasTOPS, and Castrol. Finally, in the area of vibration-based CM, the key contributors are: GE, SKF, Emerson, Rockwell Automation, and Bruel & Kjaer Vibro.
Read full chapter
URL: https://www.sciencedirect.com/science/article/pii/B9780323855105000016
Maintenance information systems
Neeraj Niijjaawan, Rasshmi Niijjaawan, in Modern Approach to Maintenance in Spinning, 2010
8.3.13 Condition monitoring
Condition monitoring is a form of predictive maintenance where continuous monitoring of the performance of machine or condition of the specific part is monitored which will affect the quality of the product. Condition-based maintenance and its associated condition monitoring procedures are ideal for spinning plant because most of the vital components earmarked for planned replacement are such that they fail gradually and progressively. These failures are truly serviceable. Failures are not mechanical failure when the machine does not stop but the quality of material processing on the machine deteriorates. For example, the metallic wire on cards, half lap and top comb needles on combers, and synthetic cots on ringframes do not break, but give poor working. Fortunately most of the major repair and replacement activities can be made condition-based rather than fixing arbitrarily their service life by choosing suitable measurement methods which are sensitive to component deterioration and/or to poor performance of the concerned machine parts.
Read full chapter
URL: https://www.sciencedirect.com/science/article/pii/B9780857090003500088
Post a Comment